Lightweight thermal insulation bricks are porous, heat-insulating bricks with high porosity, and are characterized by low thermal conductivity, low bulk density, energy saving, light weight, convenient construction, and high temperature resistance of 900°C-2000. Between °C. The main production and application of brick-shaped products is the most extensive. Lightweight thermal insulation bricks are usually classified and named according to their materials or raw materials used for their manufacture. For example, lightweight insulation bricks made of clay, siliceous, and high-alumina materials are called lightweight clay bricks, lightweight silicon bricks, and lightweight high-alumina bricks. Here are the production methods, refractoriness, and performance characteristics of various lightweight thermal insulation bricks.
Various production methods of lightweight insulation bricks:
1 Directly cut from natural porous lightweight rock into bricks;
2 Bricks made of natural or man-made porous lightweight materials;
3 Add combustible materials such as sawdust, carbonized rice hulls, polystyrene light balls into the mud, or add sublimating substances such as naphthalene, burn and volatilize to form a porous structure;
4 Add foaming agent such as rosin soap to the mud, and obtain a porous structure after firing;
5 Carbonate, aluminum powder and hydrochloric acid are added to the mud, and the gas is released through a chemical reaction to form a porous structure. In general, the second to fourth methods are more often used.
The following introduces the refractoriness and characteristics of various lightweight thermal insulation bricks:
Diatomite brick <1100°C Made from natural porous materials, it has low thermal conductivity and good thermal insulation properties.
Lightweight clay bricks are manufactured by flammability method at 1200-1400°C and are widely used.
Lightweight high-alumina bricks 1500 ~ 1350 °C foam production, heat resistance, for high temperature insulation.
Light corundum brick 1600 ~ 1800 °C Al203 content is high, the main crystal phase is corundum, can be used under reducing conditions.
Lightweight silica bricks 1220 ~ 1550 °C Load softening temperature, thermal stability.
Calcium feldspar lightweight brick 1200~1300°C The main components are CaO, Al2O3, Si02, small bulk density, good chipping resistance, and stable in reducing atmosphere.
Magnesium 1600 ~ 1800 °C Heat resistance, high temperature.
Cordierite is 1300~1500°C, small thermal expansion, good peeling resistance.
Silicon carbide 1300 °C Good resistance to erosion, good resistance to chipping, high temperature strength.
Alumina quality ≤2000°C Good thermal stability, low rate of re-calcination, use longer foaming process for ultra-high temperature furnace insulation.
Zirconite 1500 °C Low thermal conductivity, good thermal shock resistance, foam production, for ultra-high temperature furnace insulation.
Zirconia <2000°C High melting point, high resistivity, high refractive index and low coefficient of thermal expansion, produced by the foam process, for ultra-high temperature furnace insulation.
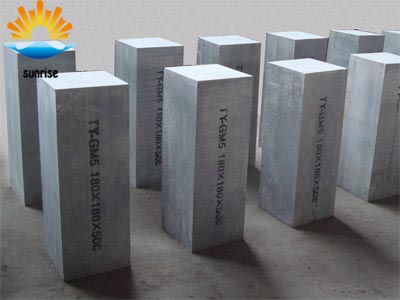