Hot blast furnace is the main equipment produced by blast furnace smelting enterprises. With the improvement of raw fuel quality and the development of injection technology, the development of hot blast furnace has become larger and larger. Because manufacturers require higher air temperatures, the overall requirements for hot blast stoves have also increased. So how should our manufacturers choose the corresponding refractory bricks and insulation materials, the refractory materials manufacturers will come to analyze with you.
At present, the refractory bricks used by hot blast furnaces of smelters are mainly clay bricks, silicon bricks and high-alumina refractory bricks (including mullite bricks, sillimanite bricks, andalusite bricks, kyanite bricks and cocoonite bricks). material. The hot air furnace's general requirements for refractory bricks are: small creep rate, good high temperature strength, and good thermal shock resistance. In addition to the above requirements, grid bricks for hot blast stoves should also have a large heat capacity. In order to be able to reasonably choose refractory bricks, they must first understand their performance, because accurate refractory characteristics are the basis for ensuring that the design is correct and reliable.
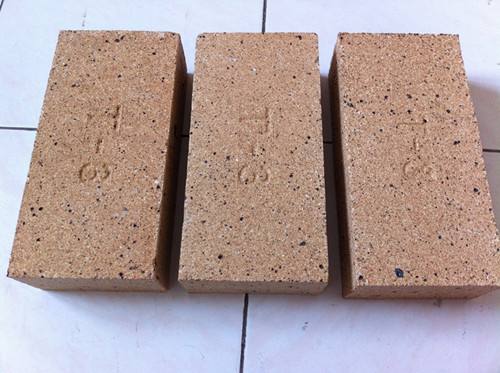
Sunrise Refractory believes that the high alumina bricks for hot blast stoves have a dense texture, high rigidity, high mechanical strength, and good abrasion resistance. The mullite bricks used by manufacturers use mullite for thermal conductivity, stable volume at high temperatures, and low creep rate. Low creep bricks made of main materials are preferred. They have high density and high temperature for hot blast stoves. , Medium temperature area. If it is used in a vault, it requires high structural strength, low creep rate, low thermal expansion rate, small chemical creep rate and high volume stability. Used as lattice brick, it has the advantages of strong erosion and thermal shock resistance. It can be built in a hot blast stove with sufficient thermal stability and high volume stability. The arch and the middle and upper part of the combustion chamber can also be used as ceramic burners for the lower part of the combustion chamber, which requires good thermal stability.
Silicon bricks used in hot-air stoves produced by refractory manufacturers have low creep rates and long-term volume stability at high temperatures. However, scaly quartz, cristobalite, and residual quartz in silicon bricks change in volume at low temperatures due to crystalline changes. There is a large change (expansion), so the thermal stability at low temperatures is poor. During use, it should be slowly heated or cooled below 800 ℃ to avoid cracks, so it should not be used in places with a sudden temperature change below 800C. Because its price is relatively cheap, it is widely used in the high temperature area of the hot air stove's vault, interconnecting tube, upper part of the combustion chamber and heat storage chamber and the upper part of the grid brick.
In addition, clay bricks used in hot blast stoves have lower fire resistance, load softening point, and creep temperature performance standards, and have good thermal shock stability. It can be widely used in non-creep rate indicators in hot blast stoves. In the low temperature region where the design and order temperature is lower than 100 ° C, the creep rate index should be increased when high density and alkali metals are used. Low-volume clay bricks can also be used for ceramic combustion.器 下。 The lower part.
If it is used on a large high-temperature hot air stove. Refractories manufacturers generally use hot-air stove high alumina brick roof, middle and upper part of combustion chamber and hot air outlet combination brick. There are mainly andalusite bricks which are made of andalusite ore and other low-creep bricks. Kyanite brick is a low creep brick made of high alumina bauxite clinker and kyanite ore. Sillimanite bricks and andalusite bricks have high fire resistance and softening temperature under load, and have good high temperature stability and thermal shock resistance. They can be used for masonry vaults, combustion chambers, upper heat storage chambers and upper grid bricks, as well as cold air inlets for ceramic burners, mixing chambers (or mixing ducts).
Finally, Sunrise Refractory Materials talk about the insulation materials for hot blast stoves, mainly some light silicon bricks and light clay bricks. The light silicon bricks have fire resistance, compressive strength, slag resistance, erosion resistance and thermal conductivity. The capacity is not as good as silicon refractory bricks, and should be built on the back of silicon refractory bricks for heat insulation. Light clay brick is a kind of light-weight thermal insulation material. It is built on the back of clay brick or light high alumina brick. It can be used as heat insulation layer. In addition, many high-aluminum refractory bricks produced by many refractory manufacturers are also good thermal insulation materials, which can be used to lay on the back of high-aluminum refractory bricks or light silicon bricks.